So I went to an open house at Angel Sword yesterday, which produces the world’s best swords. I first fell in love with their work when I saw them well over 10 years ago at Scarborough Fair Renaissance Festival in Dallas, and have schemed owning one since, which is not easy as their lowest series cost about $2,000. Of course, I could get smaller (and legal) blades from them like knives, but that’s just not the same or as fun ^_^; .
Their lowest line of swords, the Bright Knight series, holds at least the top two world records in ability from international competitions. I asked why they haven’t submitted their upper series lines (Angel Swords, Avatar series, etc) and the basic reply was “You don’t show your queens and kings if you can win with your jacks” :-). The master sword smith who started and still does most all of the work on the swords is Daniel Watson, whom has been working on swords for well over 30 years. The reason his swords are the best is that he uses combinations of ultra-tech with old tech to produce the best results. He has over 14 patents on processes and technology to produce the swords that he has been creating and refining over his lifetime that make no one able (easily) to catch up to his quality of work. The ultra-tech stuff includes cryogenics with quick freezing using liquid nitrogen and super heating, electromagnetic manipulating machines, metallurgy, and good old fashion hammer techniques, including cold forging, which most sword smiths apparently ignore.
I unfortunately had to miss a wedding of a friend of my sister’s up in Dallas for this, but I thought this more important/pressing as they only have these open houses every few [2-3] years, and I have reason to believe this may be the last one. It was supposed to start off at 9am. I got there 20 or so minutes early, well before anyone else, so I got some one on one time with Mr. Watson and another of his employees, Wolf (his real name ^_^). So I checked out his large stock of swords in the show room for the first hour or two while everyone else was arriving, and we all chatted and had general fun. There are so many beautiful swords and blades of every style, size, and make; pure works of art!
After that we went up to the forge and he did a demo with running commentary of reworking a knife, sharpening and fixing it up using types of buffers. That demonstration and everything else from the whole day was all quite fascinating. During this we also got a good list of accidents that have occurred in the shop, it was quite gruesome!!! :-D. After that we went back to the display room and had some more discussion.
Next was practical sword use ^_^. We all either borrowed swords or those who already owned ones used them, and we went out to their large front yard area (they are out in the country) and Daniel went over how to properly make cuts with a sword; proper torque and body movements to get the most out of a swing and such. Then each person that showed up (we had 10-15 people) got one wet tatami mat to practice on, which depending on your aim, one could get 5 to 10 solid cuts with. A single tatami mat, which is what most of us used, is about similar to cutting someone through the neck and a shoulder, while a double tatami mat, which they only had 1 made, is about equivalent to a solid cut through someone’s midsection. It was really fun ^_^.
We then broke for lunch with a lot more chatting about swords and many other interesting topics. The final part of the structured day was a voted upon sword creation process that we wanted to hear about. How he made his Avatar swords and the difference between the lines easily won out, as he had never released the information to anyone before (besides perhaps his apprentices and significant others). The reason he was now willing to tell us all about it was his final batch of patents on the processes went through very recently so it was safe to give it out. One of the guests video taped the whole talk, and I’m hoping to get my hands on a copy of it to post here with his permission later. He told me he wanted to edit it a bit first and show it to Mr. Watson before he did anything with it or released it anywhere. The main gist is that the lower lines just used the electromagnetic manipulation and other ultra-tech to achieve their chemical bonding properties so they can be cut to have much smaller angles on the edges without being too brittle, while the higher lines in addition have the hard work muscle and sweat forging and pounding put into them.
I think he ended his talk a little early to hit the 4pm mark when everything was supposed to end. A few people left then but I stayed around for over an hour to keep talking with the other participants. Everyone was really great and from many different walks of life and experiences all brought together by a common interest. After a few more people left, Mr. Watson brought out many of his whiskeys to let us try out. That’s the business he’s trying to break into and away from swords BTW, making whiskeys and rums and some other types of alcohol. I think I heard him mention to someone that some of the alcohols he was giving us were going for over $125 a shot!
I then left around 5pm, even though I wanted to stay longer, because I had another previous engagement I had promised to make... and then when I got there it didn’t even happen and I was quite perturbed about this, as they could have told me it wasn’t going to happen and I could have stayed at Angel Sword longer, but ah well.
I will probably be getting one of their blades very soon, as I just found out you can trade in their blades at no markdown to help get more expensive blades. So I can get a $2,000 one that I like and then have that around while I work up to a $6000 blade I really like ^_^. They also have a guarantee against breakage, chips, or damage, which is really hard to do anyways, so they can be used all you want without worry. He even showed us a sword that had been shot due to an accidental misfire of a .22 gun from the room above the show room. The sheath it was in clearly showed where the bullet went through, but there wasn’t even a ding or a scratch on the sword! The only remaining evidence was some copper that came off the bullet and etched into the metal a bit :-).
And here are all the pictures with captions that I took for the day! :-D Mouse over the thumbnails for larger copies. (Video clips to be uploaded soon.)
Show Room - Northeast corner |
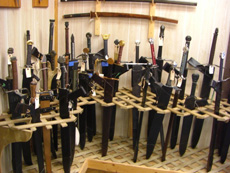 | 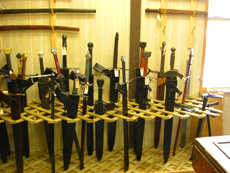 | 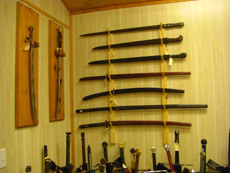 |
A large assortment of different kinds of swords. | Slightly left of the first picture, in the upper right corner are the few wakizashis on display. | Directly above the first picture. |
The left side of the last picture. These two were BEAUTIFUL. |
Show Room - Southeast corner |
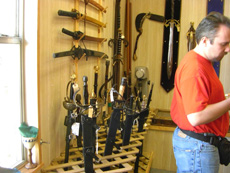 | 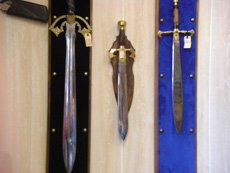 |
More assortments of swords. There were still a lot of areas in the show room I didn't even get pictures of. | The right side of the last picture. |
Show Room - West side - Katanas and Knives |
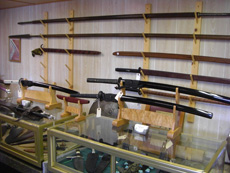 | 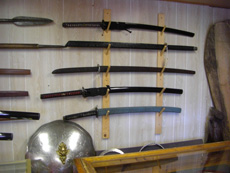 | 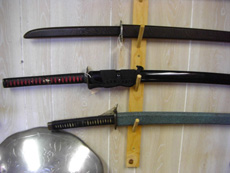 |
This whole wall was mostly katanas, with knives and other smaller blades in the glass display cases below them. Most of these swords were worth ~$3,500 a piece. | Directly to the right of the last picture. | Zoomed in from the last picture. The katana with the black and red hilt is the one I plan on getting soon, hopefully! |
The Forge - Buffers and Sharpeners |
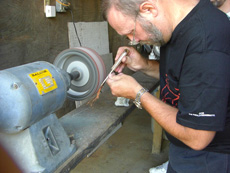 | 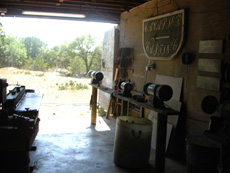 | 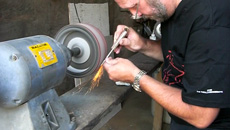 |
Dan was showing us here how he sharpens and fixes blades with the buffers. | A zoomed out (and underexposed?) view of the buffer area. To the left is a larger belt buffer for larger blades. | 3 short video clips spliced together of Mr. Watson working on a blade. |
This is the sign in the 2nd picture directly above. I believe they take it to shows as a decoration. |
The Forge - The Kiln |
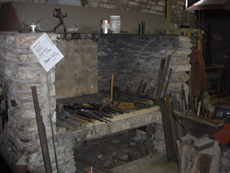 | 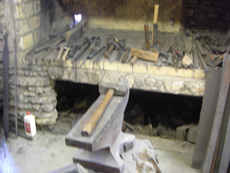 |  |
A normal heating kiln with tons of different types of hammers, tongs, and tools. | A different angle of the first picture. | This ones a little hard to see... it's a little better in my original large resolution copy. This is a shelf directly to the left of the kiln that contains racks of different types of metal sheets including (from top to bottom) steel?, brass, and copper. |
The Forge - Mr. Watson hammering |
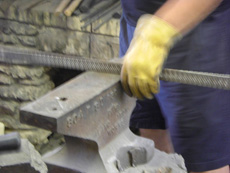 | 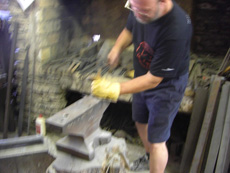 |
Hammering on a piece of steel while describing the process of creating the different series of blades. Hopefully I can get a copy of the video someone took of this later. |
The Forge - Electromagnetic Machine |
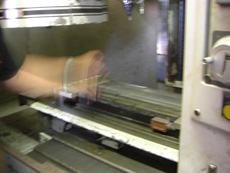 | 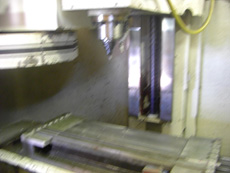 | 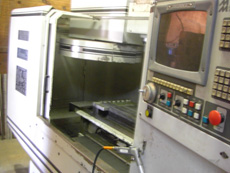 |
All 3 of these are pretty blurry, but this is the electromagnetic machine used to rearrange the molecules of the steel and do micro hammering. |
The Forge - The (High Pressure?) Furnace |
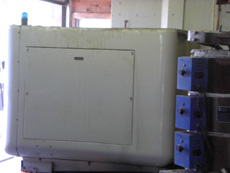 | 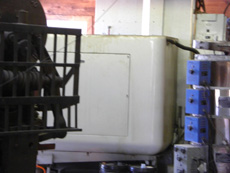 |
This is the furnace. I believe it to be super high pressure, but I know it heats steel to over, IIRC 1400 Fahrenheit. | A picture taken from the same spot as above, but shifted slightly to the left. The LOUD and powerful mechanical hammer is in the way. |
The Forge - Liquid Nitrogen tanks for cryogenics |
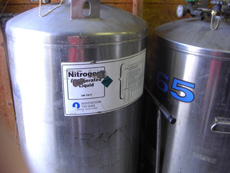 | 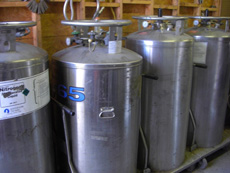 |
A close up of a liquid nitrogen tank. | All 4 (or were there 5...?) tanks sitting next to each other. |
The Forge - Unfinished blades |
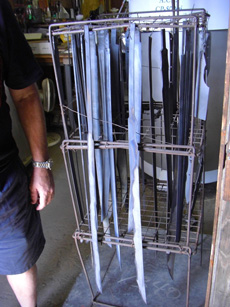 | 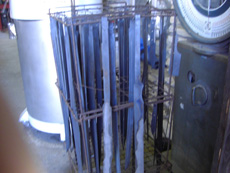 |
Blades that are being worked on. Mr. Watson is standing on the left side of the picture. He is currently standing right in front of the liquid nitrogen tanks from above. |
The Forge - Other areas |
 | 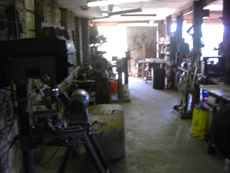 |
A workbench. This is directly to the right of the kiln, shown above. | Another area of the forge with lots of other workstations and tools. |
In the Yard - Group Photos |
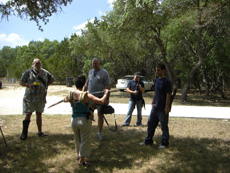 | 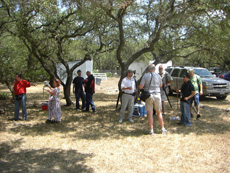 |
This was taken while we were waiting for Mr. Watson to come out and start demonstrating. | This one has most of the group that was there. The guy on the left side in the red shirt is Ingrid's husband. Lucky guy :-). |
In the Yard - Mr. Watson teaching and demonstrating |
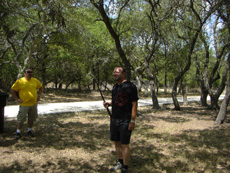 | 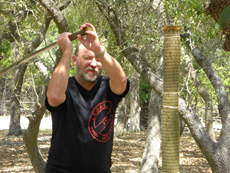 | 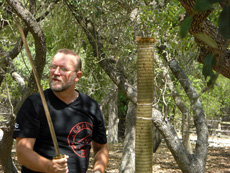 |
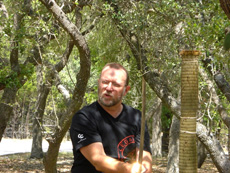 | 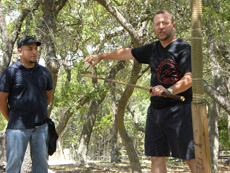 | 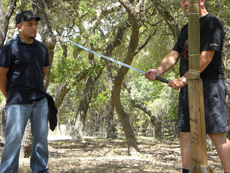 |
| Using Angel (yes that's his real name... I think) as a dummy :-) |
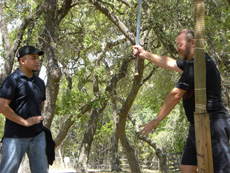 | 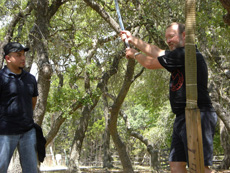 | 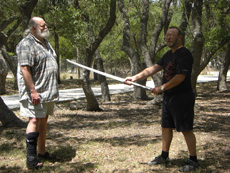 |
| Another "volunteer" 0:-) |
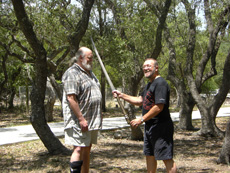 | 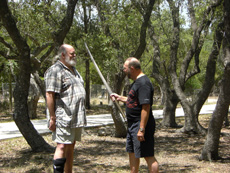 |
In the Yard - Wolf cutting (video) |
Wolf (real name) is one of Mr. Watson's employees. He did some of the first cuts, for demonstration purposes. |
In the Yard - Angel cutting |
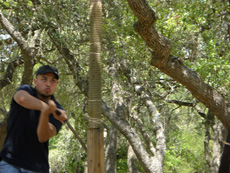 | 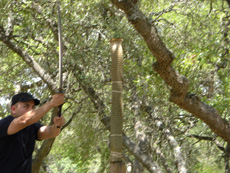 | 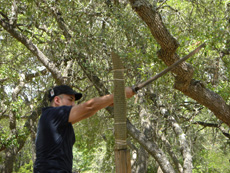 |
Angel (yes that's his real name... I think) cutting. He seemed quite good. Probably the second most experienced guest there (maybe?), after Kendall. |
In the Yard - Kendall cutting (videos) |
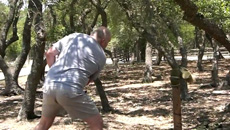 | 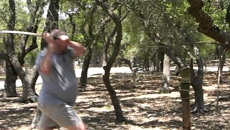 | 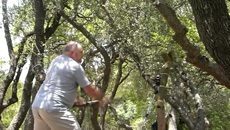 |
Kendall cutting up his tatami mat. He is apparently quite adept with swords... has won some past sword competitions and is a martial arts instructor and such. |
In the Yard - Ingrid cutting |
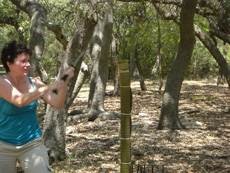 | 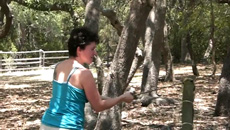 | 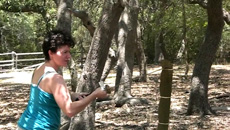 |
Girls like swords too!!! heh. You may have seen Ingrid in a few other pictures (see Group #1) with her (5 month?) old boy that she brought along. Her husband was there too, they are both great people. | Video... |
In the Office - Mythbusters Barrel |
The final picture I took. This is the .30 caliber steel barrel used in Myth Busters that they kind of cut through in an episode. |